Thermoforming vs. Injection Molding: What’s the Difference?
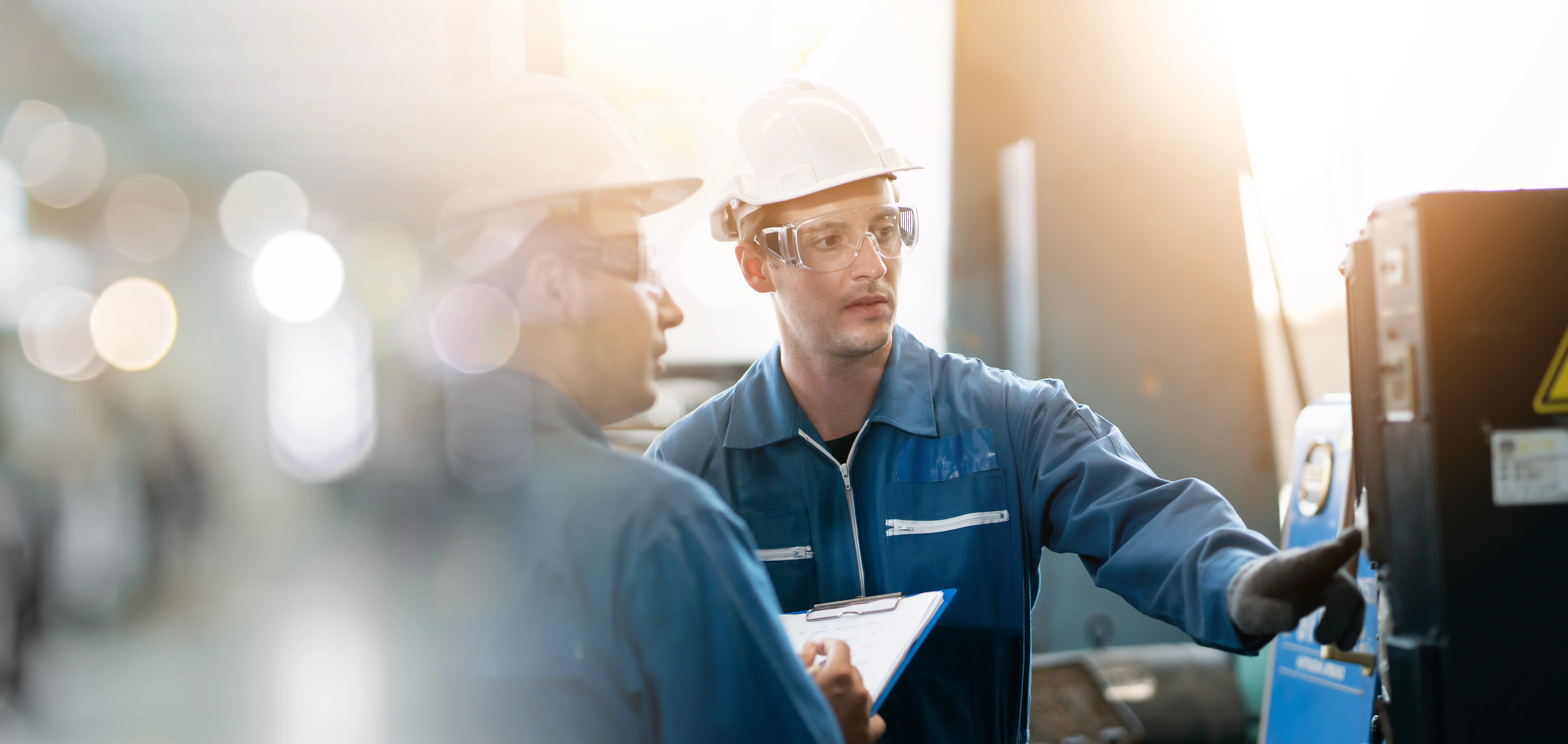
Packaging decisions are rarely just about aesthetics—they’re strategic. The materials you choose, the structure you design, and the way it’s manufactured can influence everything from cost to speed to regulatory compliance.
Two of the most common plastic packaging methods are thermoforming and injection molding. They may seem interchangeable at a glance, but under the surface, they serve very different needs.
Choosing the right process is critical. The wrong fit can drive up costs, delay your timeline, or leave you stuck with rigid tooling that limits future flexibility. Let’s explore the core differences between thermoforming and injection molding—so you can move forward with confidence and avoid costly detours.
Thermoforming vs. Injection Molding: Key Characteristics & Use Cases
While both thermoforming and injection molding can produce high-quality plastic components, the two methods approach the process in very different ways. Each has its strengths, and understanding those distinctions is key to making the right decision for your product, timeline, and budget.
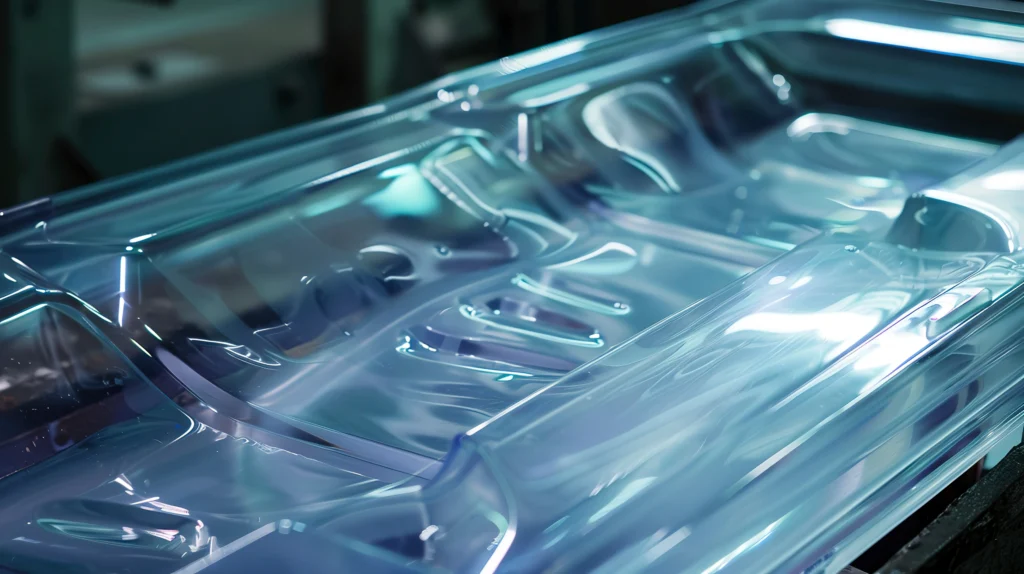
What Is Plastic Thermoforming?
Thermoforming is a manufacturing process that heats a plastic sheet until it becomes pliable, then forms it over a mold using vacuum pressure. It’s a lean, flexible approach often used when speed, adaptability, and cost control are important.
Because the tooling is less complex and faster to produce, thermoforming enables quicker iterations, more agile development cycles, and lower upfront investment, especially useful for packaging designs that may need to evolve over time.
Key characteristics:
- Lower tooling investment – Thermoform tooling is simpler and more cost-effective than injection molds, making it ideal for short to medium production runs or frequently updated products.
- Faster lead times – With shorter tooling and setup time, you can get to market faster, or pivot quickly when product specs change.
- Highly customizable for size, depth, and shape – Thermoforming allows for deep-draw designs and tailored part geometries that match your product perfectly.
- Ideal for mid-to-high volume production – Thermoforming shines in the tens to hundreds of thousands range, especially when you need a balance of performance and flexibility.
Thermoforming is a great fit when your packaging needs to be protective, visually polished, and manufactured at speed, without overcommitting to costly or rigid tooling.
Ideal use cases:
Food and Beverage Packaging: Thermoforming creates high-clarity, tamper-evident packaging that preserves freshness and shelf appeal. It uses food-safe materials and meets industry standards for retail display and consumer convenience.
Pharmaceutical Secondary Packaging: Thermoforming delivers secure packaging that protects sterile medical devices and pharmaceutical products. Custom trays and blisters ensure product integrity while meeting compliance requirements for secondary packaging
Consumer Retail Packaging: Thermoformed packaging enables eye-catching designs that boost product visibility and consumer appeal. Its versatility and quick turnaround suit fast-moving goods with shelf-ready formats like blisters and clamshells.
Electronics and industrial components: Thermoformed packaging offers ESD-safe materials and efficient nesting to protect sensitive electronics and optimize handling across manufacturing and logistics.
What Is Injection Molding?
Injection molding is a more complex process where molten plastic is injected under high pressure into a hardened metal mold. Once cooled, the mold opens and the part is ejected. This method is engineered for precision and repeatability at extremely high volumes, and it’s the go-to choice when manufacturing scale and consistency are top priorities.
That said, injection molding comes with longer lead times and significantly higher tooling costs. It also requires extensive design finalization upfront, which makes it less flexible when your product specs are still evolving.
Key characteristics:
- High upfront tooling cost – Precision molds are machined from steel or aluminum, which drives up initial investment.
- Long lead times for mold creation – Mold development often takes weeks or months, which can delay product launches.
- Best suited for large-scale runs – The economics of injection molding work best when producing millions of identical parts.
- Capable of producing complex, rigid parts with fine detail – This process excels at delivering parts with high structural integrity, tight tolerances, and intricate geometry.
Injection molding makes sense when the scale is massive, the design is fixed, and uniformity is critical to function or brand identity.
Ideal use cases:
- Housings, enclosures, or structural parts – Strong, rigid parts that serve as core product components.
- Reusable components – Think handles, caps, or parts meant for long-term use rather than single-use packaging.
- Extremely high-volume projects – Products with consistent form and mass distribution requirements benefit most from injection molding’s repeatability.
How to Decide Between Injection Molding and Thermoforming
There’s no one-size-fits-all answer—your ideal manufacturing process depends on what you’re packaging, how quickly you need it, and how much you plan to produce.
While both thermoforming and injection molding have their strengths, your decision should align with your project’s priorities.
Ask yourself:
- What volumes are we producing?
Thermoforming typically makes more sense for runs in the tens to hundreds of thousands. If you’re manufacturing in the millions, injection molding may offer better long-term cost efficiency.
- How likely is the design to change?
Thermoforming is ideal when product specs may evolve. Its faster tooling allows for quicker iteration and updates. Injection molding is better for locked-in, stable designs.
- How important is speed to market?
Need to launch quickly? Thermoforming offers shorter lead times for tooling and production, helping you get to shelf faster.
- What kind of part complexity do we need?
Intricate, rigid components with internal geometries might require the detailed capabilities of injection molding. Custom-formed trays, blisters, and open-faced designs are better suited to thermoforming.
Once you’ve clarified these needs, you’ll be in a better position to weigh the trade-offs of each process and choose a partner who can help you make the most informed call.
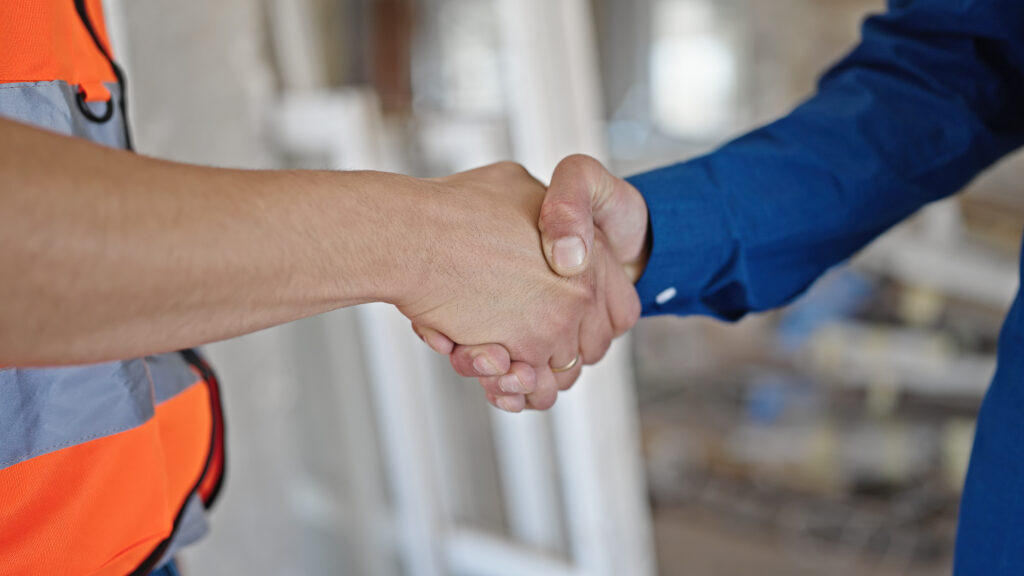
Selecting the Right Process Starts With the Right Partner
You don’t have to make the decision alone. At Elmes, we work closely with product and engineering teams to assess requirements, evaluate trade-offs, and guide you toward the most efficient path forward—whether that’s thermoforming or another solution entirely.
If you’re navigating tight timelines, evolving product specs, or industry-specific requirements, thermoforming might be the strategic edge you need. And with Elmes, you’re not just getting a packaging vendor—you’re getting a partner who understands your product, your pressures, and your goals.
Let’s talk about overcoming your next packaging challenge.