Solving Packaging Challenges for a Global Auto Leader
Discover how Elmes Packaging solved complex challenges for a global automotive manufacturer with speed, precision, and reliability.
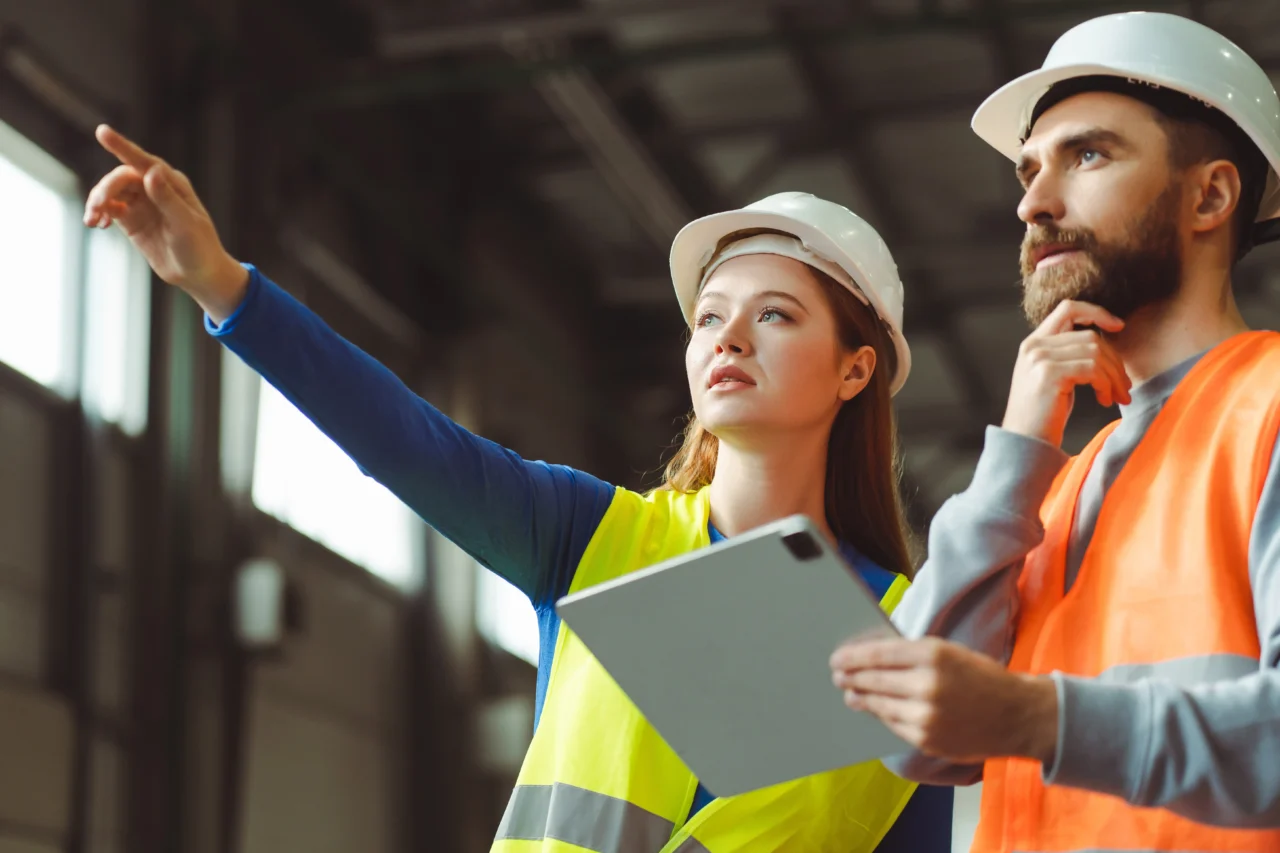
Case Study: Overcoming Critical Packaging Challenges with a Global Automotive Manufacturer
A globally recognized leader in automotive manufacturing headquartered in North America — specializes in engine and transmission pumps and powder metal components. Operating with an uncompromising commitment to precision, efficiency, and quality, this manufacturer plays a crucial role in advancing automotive technology worldwide.
Elmes Packaging has built its reputation on solving the toughest packaging challenges with speed, ingenuity, and an unwavering commitment to product protection. Working closely with the client’s senior engineers, Elmes not only redesigned the faulty tray, but also continues to provide fast, cost-effective, and highly customized solutions that ensure their partner can focus on what they do best — delivering cutting-edge automotive components to market.
However, in an industry where exacting standards are non-negotiable, even minor packaging flaws can have significant consequences. Ensuring that precision-engineered components arrive intact and undamaged is critical to maintaining production timelines and product integrity. When this company encountered recurring packaging challenges — most notably a tray design that was inadvertently damaging their own products during transport — they turned to a trusted partner: Elmes Packaging.
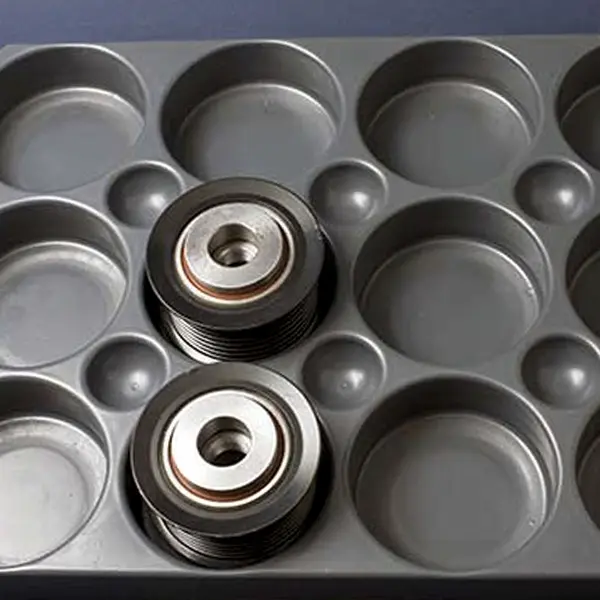
The Challenge
In the fast-moving world of automotive manufacturing, packaging is more than just basic product protection — it’s a critical component of the supply chain. This manufacturer needed a packaging partner that could rise to the challenge whenever issues arose.
Key Packaging Challenges:
- Ongoing Design Modifications: Automotive components are frequently updated to improve performance, requiring packaging that evolves alongside the products.
- Product Damage in Transit: The client had internally designed a manufacturing tray, but it was inadvertently causing chipping and damage to their precision parts during transport.
- Balancing Cost and Performance: They needed solutions that provided top-tier protection while remaining cost-effective — a balance that not all suppliers could deliver.
- Speed and Responsiveness: Any delay in resolving packaging issues could slow down production and impact delivery schedules, making a fast and reliable packaging partner essential.
With these challenges in mind, the automotive manufacturer required a partner who could think fast, adapt quickly, and engineer solutions that truly protected their products.
Elmes’ Solution
As a leader in custom thermoformed packaging, Elmes Packaging stepped in with their signature problem-solving mindset and engineering expertise. Instead of offering a one-size-fits-all approach, Elmes worked directly with the client’s senior engineers to understand the root cause of their packaging issues and develop a solution that met the highest standards of protection and performance.
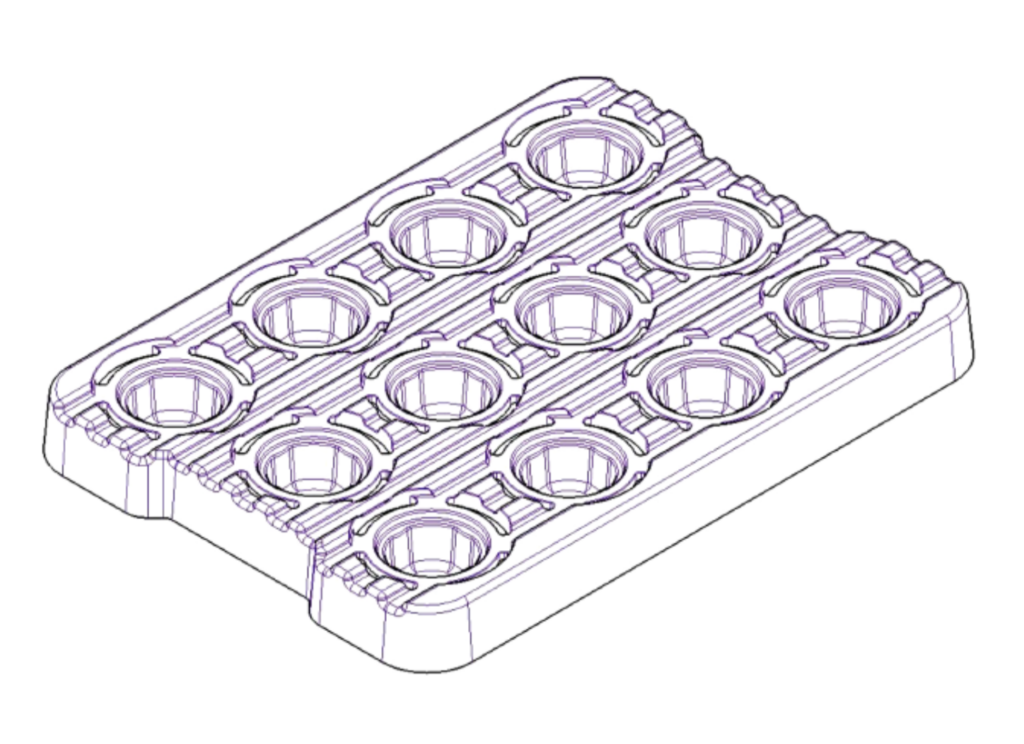
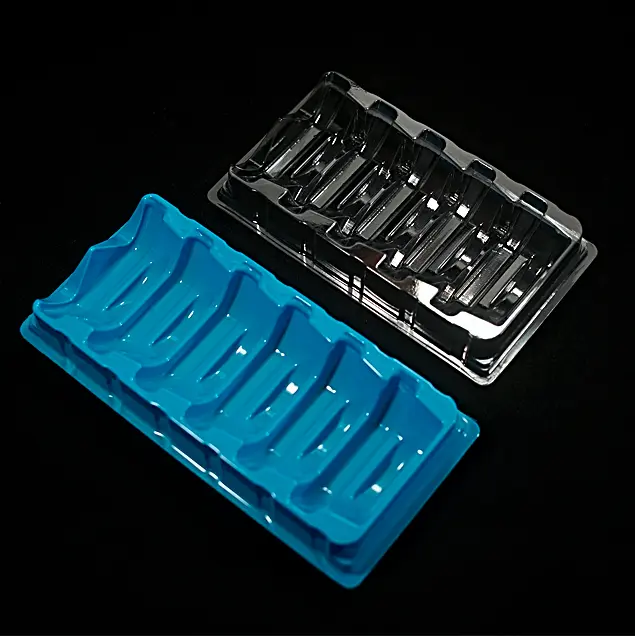
Innovative Custom Modifications
The client’s original manufacturing tray, while structurally sound, was inadvertently causing damage to precision parts during transit. Rather than completely discarding the design, Elmes proposed targeted modifications:
- Structural Adjustments: Modifications to the tray’s design reduced the risk of product chipping.
- Precision Engineering: The updated tray balanced rigidity with protective cushioning, securing components more effectively in place.
- Collaborative Approach: Elmes’ engineers worked hand-in-hand with the client’s team to ensure the modifications aligned with production requirements.
Responsiveness and Reliability
In automotive manufacturing, timing is everything. Every delay in production or shipping can cause a ripple effect across the supply chain. Elmes’ ability to rapidly address challenges and iterate on solutions made them an indispensable resource for the client.
- Quick Turnaround: Elmes worked swiftly to assess the problem and implement modifications, preventing costly delays.
- Trusted Problem-Solvers: Instead of simply providing packaging, Elmes positioned itself as an extension of the client’s engineering team — anticipating challenges and offering proactive solutions.
- Always Ready: The client knew that whenever a packaging issue arose, Elmes would be there with an answer.
Value and Cost-Effectiveness
Investing in an entirely new packaging system wasn’t a practical option. The client needed a solution that balanced cost with high performance.
- Maximizing Efficiency: Instead of completely overhauling packaging designs, Elmes provided targeted modifications that resolved issues without unnecessary costs.
- Long-Term Cost Savings: The improved packaging not only protected products better, but also reduced waste and the need for replacements.
- Competitive Pricing: By leveraging decades of expertise, Elmes provided a solution that delivered both quality and value.
Results & Impact
Through Elmes’ strategic, problem-solving approach, the client was able to overcome their key packaging challenges and enhance their overall supply chain efficiency.
Key Outcomes
✅ Product Integrity Restored — The modified tray design eliminated chipping and damage, ensuring components arrived in pristine condition.
✅ Production & Shipping Efficiency Improved — By solving the packaging issue quickly, the client avoided costly production delays and supply chain disruptions.
✅ Stronger Partnership Built — The client now relies on Elmes as their go-to packaging problem-solver, ensuring that future packaging challenges are met with expertise and speed.
“Elmes Packaging always listens to our concerns and quickly shares the options to solve any issue. What sets them apart from other packaging suppliers we’ve worked with is how responsive they are — they always respond within a day and, if necessary, will visit our plant to make sure they have the best understanding of our requests. Moreover, their products are of very good quality, and they always provide different options for customizing the design. I would 100% recommend Elmes to other manufacturers because they will always work with you to find the best solution to your packaging issues.”
— Manufacturing Engineering Specialist, Global Automotive Manufacturer
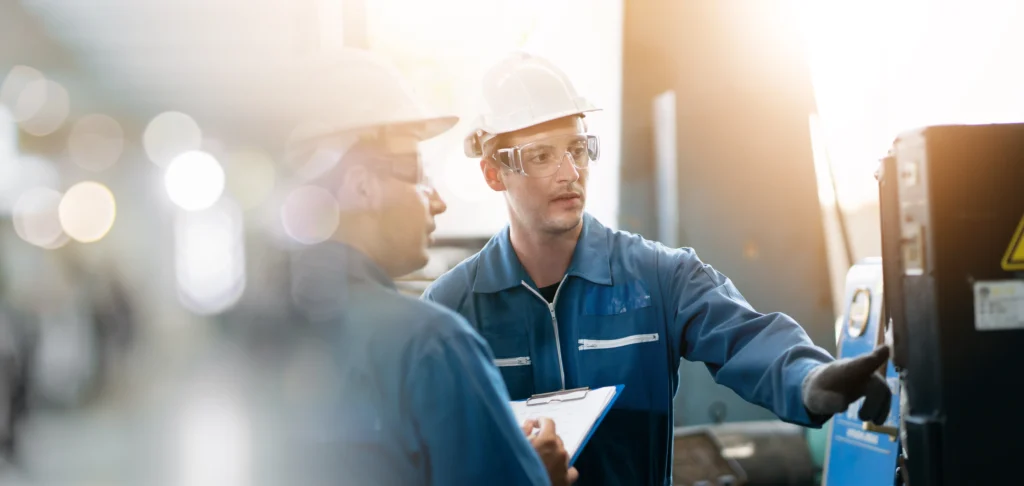
A Partnership Built on Problem-Solving and Performance
At Elmes Packaging, the mission is clear: Protect. Perform. Solve.
For this manufacturer, Elmes didn’t just provide a product — they provided a solution. By stepping in when challenges arose, adapting packaging design with speed and expertise, and delivering unmatched responsiveness, Elmes proved to be more than a supplier — they became a trusted partner.
In industries where precision matters and quality is everything, Elmes Packaging delivers solutions that perform — every time.
Let’s Create Something Great Together
We’re here to help answer your general inquiries or questions related to your next thermoforming project.
You can also request a quote and a member of our team will be in touch within 1-2 business days.